Manual: Terex TL120 Wheel Loader – Operation & Maintenance Instructions
Free Download Manual: Terex TL120 Loader – Operation, Maintenance, Safety, Specifications & Troubleshooting in Full PDF.
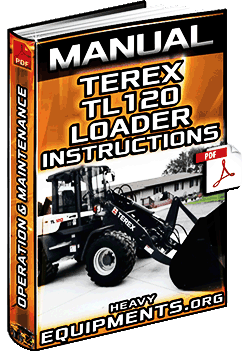
Full Manual – Learning
TEREX TL120 WHEEL LOADER
OPERATION & MAINTENANCE
Operating Instructions, Introduction, Warranty and Maintenance, Copyright, Notes on Using the Operating Manual, Regulations Concerning Environmental Protection, Pictograms, Safety and Accident Prevention, Declaration of Conformity, Introductory Remarks, Proper Use, General Safety Instructions, Operation, Danger Zone, Transport of Persons, Stability, Driving, Operation, Guides, Danger of Falling Objects, Working in the Vicinity of Underground Power Lines, Working in the Vicinity of Overhead Power Lines, Operation in Closed Spaces, Work Stoppages, Change of Work Attachments, Maintenance, Repair, Recovery, Loading and Transportation, Monitoring and Inspections, Fire Protection, Emergency Exit, Notes Concerning Residual Dangers, Technical Specifications, Views, Dimensioned Drawing with General-Purpose Bucket, Dimensioned Drawing with Multi-Purpose Bucket, Dimensioned Drawing with Fork Lift Attachment, Engine, Electrical System, Travel Drive, Brakes, Hydraulic System, Axles, Tires, Fuels, Lubricants and Coolants, Fluid Capacities, Fuel, Lubricant and Coolant Specifications, Permissible Loads in Compliance with German Road Traffic Regulations (STVZO), Sound Level Values, Vibration, Dimensions and Weights, Optional Accessories, Operation, Initial Familiarization, Display Elements and Operator Controls, Engine, Starting, Monitoring the Machine During Operation, Switching Off the Engine, Driver’s Seat / Steering Wheel Tilt Adjustment, Heating/Ventilation, Lighting in Compliance with German Road Traffic Regulations (STVZO), Hydro-Inflation of Tires, Driving, Steering and Braking, Driving, Steering, Brakes, Driving on Roads, Switching Off the Machine (Parking), Working Operation, Operation – Loader, Changing Work Attachments, General, Assembly of Work Attachments, Notes on How to Work with the Machine, Loading, Scraping and Grading, Excavating, Recovery, Loading and Transporting, Recovery, Loading with a Crane, Transport of the Machine, Care and Maintenance, Intervals, Regular Oil Analyses, Warranty, Inspection Parts and Aids, Care and Cleaning, Notes for Operation in Winter, Checking, Maintenance and Inspection Plans, Initial Inspection (Hand-Over Inspection), Daily and Weekly Tasks, Overview of Lubricating Points, Inspection Plan, Inspection and Maintenance Work, Engine Oil, Changing the Engine Oil Filter, Cooling System, Combined Hydraulic Oil-Water Cooler, Fuel System, Air Filter, Air Intake, Double V-Belt, Checking the Valve Lash, Brakes, Hydraulic Oil Tank, Hydraulic Oil Return Filter, Replacing the Breather, Axles, Wheels, Injection Valves, Electrical Equipment, Cab Ventilation Dust Filter, Windshield Washer System, Immobilization, Preservation (Temporary Immobilization), During the Immobilization, After Immobilization, Trouble-Shooting, Engine, Table of Faults…
- Pages: 108
- Size: 5.64 MB
- Format: PDF (Adobe Reader)
MANUAL – TEREX – WHEEL LOADER – OPERATION – MAINTENANCE INSTRUCTIONS – SAFETY – ACCIDENT PREVENTION – TECHNICAL SPECIFICATIONS – WORKING OPERATION – RECOVERY – LOADING – TRANSPORTING – CARE – RECOVERY – TROUBLESHOOTING
FREE MANUAL FOR TEREX WHEEL LOADERS PROFESSIONALS – LEARNING